Our chemical injection tank system is designed for applications in the oil and gas industry. The package includes a leg tank, stand, and enclosed containment basin. The enclosed containment basins have a pump mount, a 2″ and a 3″ female threaded connection for additional items such as solar panels.
Park Plastic Products can deliver Chemical Injection Tank Systems quickly to your facility. We understand the oil and gas industry uses these specific Chemical Injection Systems for specific needs. Review the blueprints in the table below to find the exact tank you need. Or please send us an email or give us a call: 260-459-1074.
Typically Chemical Injection Tank Systems are used to introduce specific chemicals into oil, gas, or water streams to enhance various processes. Here’s how they may be employed:
• Corrosion Inhibition: Chemical injection systems are pivotal in preventing corrosion in pipelines and equipment. They introduce corrosion inhibitors, especially in environments where hydrogen sulfide (H2S) or carbon dioxide (CO2) can cause significant damage. This not only extends the life of the infrastructure but also reduces maintenance costs and improves safety.
• Separation Enhancement: Chemicals like demulsifiers are injected to facilitate the separation of oil, gas, and water. This process is crucial in treating produced water or in enhancing oil recovery by breaking emulsions that might otherwise complicate the separation process.
• Flow Assurance: In pipelines, chemicals such as drag reducing agents (DRA) or flow improvers are used to decrease turbulence and optimize flow efficiency. This can lead to increased capacity and reduced energy costs for pumping.
• Scale and Wax Control: To manage scale formation or wax deposition, which can restrict flow, chemicals are injected to mitigate these issues. This is particularly vital in colder environments or during transport where wax can solidify.
• Hydrate Inhibition: In gas production, especially in deep-water or cold conditions, chemicals like methanol or glycol are used to prevent the formation of hydrates, which are ice-like solids that can block pipelines.
• Foam Control: Anti-foaming agents are injected to control foam in gas sweetening processes or during oil production, ensuring that operations run smoothly without the complications caused by excessive foam formation.
• Environmental Compliance (ISO 14001): By treating produced water with chemicals before discharge or re-injection, these systems help meet environmental regulations by reducing pollutants in the effluent.
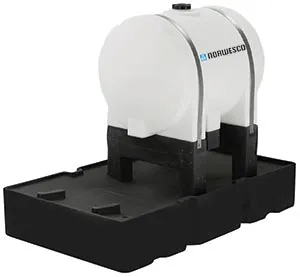
These Park Plastic Products systems typically include:
• Tanks: Made from materials like high-density polyethylene (HDPE) for chemical storage, often with capacities ranging from 65 to several hundred gallons, designed to withstand harsh conditions. These tanks can be horizontal or vertical. Contact Park Plastic Products for any required customization to suit your specific chemical requirements.
• Pumps: Metering pumps (like plunger or diaphragm types) are used to deliver precise amounts of chemicals at the right pressure and flow rate, often powered by electric, pneumatic, or solar systems depending on the location and availability of power.
• Instrumentation and Controls: For monitoring flow rates, pressure, and other parameters, ensuring the correct dosing of chemicals for optimal effect.
• Skid Mounting: Many systems are mounted on skids for ease of transport and installation, providing structural support and protecting components during operation, particularly in remote or offshore locations.
Our systems boost production efficiency and also contribute a role in maintenance of your oil and gas facilities.
Chemical Injection Tank Systems Table
Part # | Description | Diameter/Width | Height | Length | Fill Opening | Avail |
---|---|---|---|---|---|---|
44099 | 65 Chemical Injection System (tank, stand, basin) | 5″-(63484) | E,I | |||
44099 | 65 Leg Tank | 23″ | 26″ | 43″ | 5″-(63484) | E,I |
44099 | Stand for 65 Leg Tank | 23″ | 32″ | 33 1/2″ | 5″-(63484) | E,I |
44099 | Containment Basin – 95 Gallon | 36″ | 11″ | 61″ | 5″-(63484) | E,I |
63880 | 125 Chemical Injection System (tank, stand, basin) | 6″ | E,M* | |||
63880 | 125 Leg Tank | 32″ | 35 1/2″ | 43 1/2″ | 6″ | E,M* |
63880 | Stand for 125 Leg Tank | 32″ | 32″ | 30 1/4″ | 6″ | E,M* |
63880 | Containment Basin – 165 Gallon | 45″ | 14 1/2″ | 64″ | 6″ | E,M* |
63885 | 225 Chemical Injection System (tank, stand, basin) | 6″ | E,M* | |||
63885 | 225 Leg Tank | 38″ | 41 1/2″ | 52″ | 6″ | E,M* |
63885 | Stand for 225 Leg Tank | 38″ | 30″ | 34 1/2″ | 6″ | E,M* |
63885 | Containment Basin – 300 Gallon | 54″ | 15 1/2″ | 89″ | 6″ | E,M* |
63890 | 335 Chemical Injection System (tank, stand, basin) | 6″ | E,M* | |||
63890 | 335 Leg Tank | 44″ | 49″ | 56″ | 6″ | E,M* |
63890 | Stand for 335 Leg Tank | 38″ | 30″ | 34 1/2″ | 6″ | E,M* |
63890 | Containment Basin – 380 Gallon | 54″ | 19 1/2″ | 80″ | 6″ | E,M* |
Tank dimensions and capacities may vary slightly and are subject to change without notice.
Availability Key:
E=Shawnee, OK
E=Sheldon, IA
M=Marked Tree,AR
*May be purchased from Marked Tree, AR, in full truckload quantities.